Nuclear reactor and primary coolant system
The fuel assemblies which form the reactor core, are loaded into a specially fabricated cylindrical steel pressure vessel (the reactor pressure vessel). The reactor pressure vessel is about 12 metres high and has a 20 cm thick steel wall with an inner diameter of about 4 metres. It weighs about 314 tonnes. The primary coolant system of a 900 MW class reactor consists of the reactor pressure vessel and the primary circuit with 3 identical loop. Each loop has a primary coolant pump, a steam generator and the interconnected piping. A pressuriser is installed in one of the 3 loops. Each primary coolant pump will circulate the cooling water (ordinary water) around the loop through the reactor core at a high pressure of about 155 bar (1 bar = 100 kPa). In addition to its moderator function, the cooling water would also transfer the heat from the reactor core to the steam generator. The water temperature at the reactor pressure vessel outlet is about 330 degree C whereas the water temperature at the inlet of the vessel is about 290 degree C. The cooling water is in a sub-cooled condition at such high temperature and pressure to prevent it from boiling. The steam generator of about 20 metres in height is fitted with U tubes in the inside which serve as the heat exchanger to transfer the heat from the water in primary circuit to that in the secondary circuit. The heat will convert the feed water in the secondary circuit to steam for driving the turbine-generator.
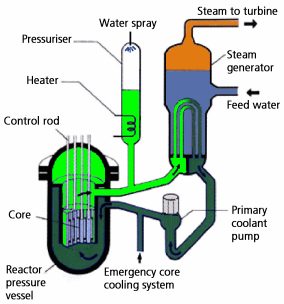
Primary Coolant Circuit
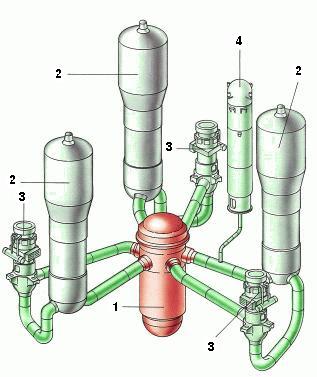
Primary Coolant System
- Reactor Pressure Vessel
- Steam Generator
- Primary Coolant Pump
- Pressuriser
The pressuriser is mainly used to maintain the pressure in the primary coolant circuit and prevent overpressure. It is a cylindrical pressure vessel of about 2 m in diameter and about 13 m long, tapping off from one of the hot legs in the primary loops. The steam and water volumes occupy the top half and bottom half of the pressuriser respectively during normal operation. There are water spray nozzles at the top and a group of heaters at the bottom of the pressuriser. The water level inside the pressuriser and thus the pressure in the primary coolant circuit can be controlled by operation of the heaters and water spray. A sophisticated pressuriser level control system is used to regulate the water level inside the pressuriser so as to ensure a proper pressure control during reactor power change and transient plant operation. The heaters will be turned on to increase steam production if the pressure drops. If the pressure increases, the water spray will be turned on to condense the steam to reduce the pressure. In addition, the control system will provide a protection signal to shutdown the reactor automatically if the pressure inside the pressuriser is too high or too low.